- T Slots And Clamps Or Vacuum Pump For Cnc Machining Machine
- T Slots And Clamps Or Vacuum Pump For Cnc Machining Machines
- T Slots And Clamps Or Vacuum Pump For Cnc Machining Tools
Holding your workpiece securely is essential to a successful project. In this post, I’ll discuss seven proven methods to hold your workpiece so you can cut it accurately. I’ll introduce each method, then summarize the pros and cons of each.
A common and simple way to hold down a piece is with slotted clamps. You simply place the clamp on top of the workpiece then put the clamp screw through the slot. The clamp screw must thread into the machine’s bed. The M3 has a grid of sixteen points for fastening while the Carve King uses T. 58Pcs Clamping Kit Set for Drilling Milling Machine T-Slots Step Block Clamping. NEW Portable Milking Machine 250L/min Vacuum Pump for Cow Goat Milking Machine. CNC 3018 PRO Machine Router 3 Axis Engraving DIY Wood Milling Cut +5500mW Laser. Custom T-Slot Plates. Our exclusive custom design and manufacturing process allows you to have your own custom T-Slot Plate. Discuss your requirements with our engineers and technical team, we can provide 3D CAD drawings or supply us with a CAD file you need. We can help create your exact requirements and the perfect T-Slot plate for your CNC.
Top Clamping
A common and simple way to hold down a piece is with slotted clamps. You simply place the clamp on top of the workpiece then put the clamp screw through the slot. The clamp screw must thread into the machine’s bed. The M3 has a grid of sixteen points for fastening while the Carve King uses T track extrusions. The Power Route gives “infinite” fastening options with its full T Plate bed.
It is best to have a shim piece on the backside of the slotted clamp approximately equal to the thickness of the material. Examine the workpiece prior to clamping it down. Many workpieces will have some bow before you even clamp it. With this method, you should put the convex side face down, so the edges are raised up from the surface. The clamps help pull the bow out. This video of the Power Route cutting aluminum shows the top clamping method in practice. We include a set of water jet cut slotted aluminum clamps with every machine bundle that we sell.
Pros: Fast and easy.
Cons: Can actually add bow to the material depending on how it is clamped. Limited access to edge of stock. Heavy cuts can push the workpiece.
Edge Clamping
Edge clamping is a less commonly used method, but still should have a place in your workholding toolbox. This method involves applying pressure to the part from opposing sides in a similar way that a vise holds stock (more on vises in a moment). There are a couple ways to achieve this. You could make yourself some toe clamps, as described in this Instructable. We have eccentric spacers if you want to build some of the clamps described there. Another inexpensive edge clamping solution is to use blocks and wedges. You can find files for them here and cut them yourself. With blocks and wedges, you simply fix one block in place, then slide the stock up to it. On the opposite side, you fix another block to the table and leave a little space for the wedge to get between your stock and the block. You then press or gently tap the wedge in with a mallet. Press down on the material as you work the wedge in to make sure that it hasn’t lifted the material from the bed or spoil board.
Pros: Full access to top of piece. Quick if you have a good system.
Cons: Can add bow to thinner or less sturdy material. Less secure than vise workholding.
Vacuum Clamping
Vacuum clamping is one of the most mesmerizing and effective methods. Let’s start with a little science so we can better understand the power of vacuum clamping. Everything around you is exposed to about 14.7 pounds per square inch of air pressure. That’s just the air pressure here on Earth, at least around sea level. The “magic” of vacuum workholding is that it removes most of that pressure from one side of the piece. I say “most” of that pressure because the vacuum system probably won’t be completely efficient. Let’s suppose that you achieve just 80% of a perfect vacuum and that your workpiece is 5 inches by 5 inches (25 square inches). 80% times 14.7 PSI times 25 inches equals 294 pounds of hold down force. What if instead the work piece is 10 inches by 10 inches? The hold down force increases to 1,176 pounds! If you tried to push the work piece off the vacuum plenum, you’d literally push your machine off the table without the work piece ever budging. Some vacuum systems require a large vacuum pump, but our vacuum clamping system uses your air compressor to generate vacuum with a venturi vacuum generator. Just arrange the gasket material in the vacuum plenum to match the shape of your part, put on your work piece, and turn the valve on the venturi vacuum generator.
Pros: Very quick to take parts on and off. Sucks material completely flat. Generates an extreme amount of holding force. Allows full access to the top of the work piece.
Cons: You can cut all the way through your material, but you need to be strategic about where your gasket material is placed relative to the profile. Alternatively, you could leave a few thousandths of an inch of material at the bottom so as not to break the vacuum seal. Really small pieces can’t be clamped.
Vise
A vise is commonly used in metalworking on industrial mills, but this may be the best way to hold a piece you are cutting too. The challenge in CNC router applications is using a vise that is low profile enough to allow gantry clearance. A drill press vise is excellent for the Carve King and Power Route, while the M3 probably won’t have enough clearance. An added bonus of using a vise is that you can designate the corner of the fixed jaw of the vise as an origin of a work coordinate system if you have homing switches (Side note: See this video for everything you wanted to know about work coordinate systems). This will allow you to perform repeated work quickly.
Pros: Immense amount of holding force. Very quick to clamp and unclamp work. Allows full access to top of work piece.
Cons: Only relatively smaller pieces can be held. Accidentally colliding with an iron vise isn’t fun. Thinner or weaker materials will surely bow or collapse.
Direct Fastening
Direct fastening is just what it sounds like. You simply screw the stock down directly. You can run a wood screw through your material and into your spoil board or you can pre-drill the stock and run machine screws or bolts through the material and fasten it to the table directly. I sometimes use this method in conjunction with another.
Pros: Great way to “tack down” thin parts in the center when another method can’t. Allows you to profile the outside of a piece if edge clamping or top clamping would interfere.
Cons: Can take longer than other methods to set work up. You must plan your cut paths not to collide with any screws placed within the cut boundaries.
Double Sided Tape
T Slots And Clamps Or Vacuum Pump For Cnc Machining Machine
Double sided tape is a favorite method among home PCB fabricators. You must clean the bottom of the work piece as well as your table or spoil board to make sure it sticks. You’ll want to select a strong tape and be careful in applying it so as not to put any wrinkles in the tape. Press firmly down on the workpiece for 10 or15 seconds to make sure it’s stuck well.
Pros: Flattens out thin work pieces such as printed circuit boards. Allows access to the entire top side of work piece.
Cons: You will be left with adhesive residue that needs to be cleaned up. Does not always provide a firm hold down.
Painters Tape and Superglue
A closely related method is to use painters tape and super glue. You start by cleaning both the table or spoil board surface and the workpiece surface. The surface should be free of dirt, burrs, and debris. Apply blue painters tape to each surface. Use wide tape. Lay down each strip right at the edge of the last, but don’t overlap them. Use a putty knife or straight edge to remove any air bubbles and completely flatten the tape. Apply a quality superglue to one side and press the work piece down to the table. Hold it down with your own pressure for about a minute as the glue sets. You may want to put a weight on top of the work piece for a couple more minutes as the glue further sets.
Pros: Provides a very firm hold. Flattens out bowed pieces. Allows access to the entire top side of work piece.
T Slots And Clamps Or Vacuum Pump For Cnc Machining Machines
Cons: Can take a little while to set up. Potentially messy. Can be hard to get the material back up.
Which is right?
In many workholding cases, there is no right answer. There is usually a wrong answer though. You can’t hold a sheet of thin aluminum with a vise, but you could probably vacuum clamp or direct fasten it. Similarly, you couldn’t vacuum clamp a 1” inch cube, but the vise or edge clamping would do well. Each method has its place. Be sure to try a few of the different methods to see what works best for you in each situation.
T Slots And Clamps Or Vacuum Pump For Cnc Machining Tools
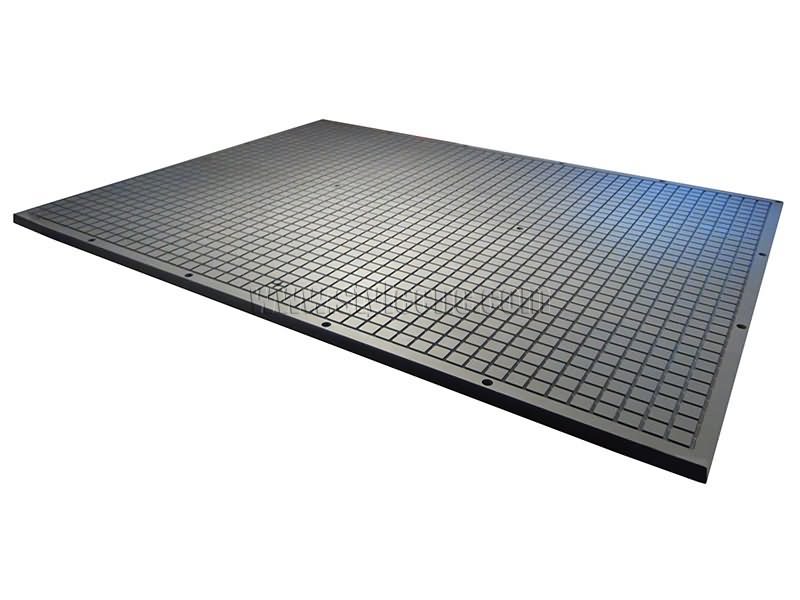
Leave a comment to tell us which methods you prefer and be sure to subscribe in the footer if you haven’t already.